Drive Train detail
- Captain Edward
- Apr 17, 2018
- 6 min read
Updated: Apr 23, 2018

Car 30 Team - soon to be renamed “The Falcons"
Happy Easter to y’all. Below I continue my weekly update to the team and a growing list of previous and future team participants who may find the progress interesting to follow, even if they have hung up their Rhino Charge boots.
Last week was a short week so limited progress in the garage. That said the positioning of most of the chess pieces in the rear section is complete and now it is a case of getting the various bits of metal cut, welded and/or bolted down. This week's focus is on getting the fuel flowing, the batteries and fuel pumps in place and the vehicle functional so that the Falcon can get out of the yard and onto the road as soon as possible. We will fit the padding and accessories later!
The Drive Train
As a non-mechanically minded person, the drivetrain has been one of the longest learning curves for me over the years, culminating in a disastrous outcome in 2016 when lots of metal stuff inside the axles were ripped to shreds!!
We started in 2006 with a normal Range Rover and as the years have passed we have upgraded different sections of the whole mechanism that takes the power from the engine all the way through to meeting friction on the ground. The important part to remember is that the weakest link is what breaks first….!
Below I have detailed out how the drive train works, what the Falcon’s drivetrain looks like today, some possible improvements that the funds raised are being allocated to and a number of the sorry stories that have happened when each of the different parts has failed us on previous Charges.
Feel free to skim it if mechanics bore you but at least readers will begin to realise the extent to which we will be putting this vehicle under enormous strain on the day. Mechanical failure is highly likely but we plan as meticulously as we can to avoid this.
DriveTrain: Basic Overview
1) Engine takes power to a gearbox/transmission
2) Gearbox and transmission drives propellor shafts (rear and front)
3) Prop shafts attach to differentials which switch power 90 degrees
4) Half shafts run inside front and rear axles and attach to hubs
4) Hubs attach to and turn wheels
5) Wheels meet varying resistance in off-road conditions
Prop Shafts

As those who watched the movie link I sent last week will know, in 2006 we snapped the rear prop shaft that takes power from the gearbox to the rear axle. After this happened, I took the twisted stub and mounted it on a piece of wood and donated it for what is now an annual Rhino Charge prize “The Properly Shafted Award”. The Falcon currently sports a front prop shaft from a LandCruiser and a standard Range Rover rear prop shaft.
I am looking into getting strengthened versions for at least the rear prop shaft!
Differential
When the power reaches the axle, it needs to be converted 90 degrees to turn the half shafts that run inside the axle. This works by the prop shaft being attached to a gear (pinion) which meshes with another gear (crown wheel). In 2016 we replaced the crown wheels with a different gearing ratio to compensate for bigger tyres, but in error we used standard Landrover 109 diffs. When put under strain, the rear crown wheel and pinion gears lost their positioning and ripped each other to shreds. This happened the afternoon before the Charge and so we did not even start the race in 2016!
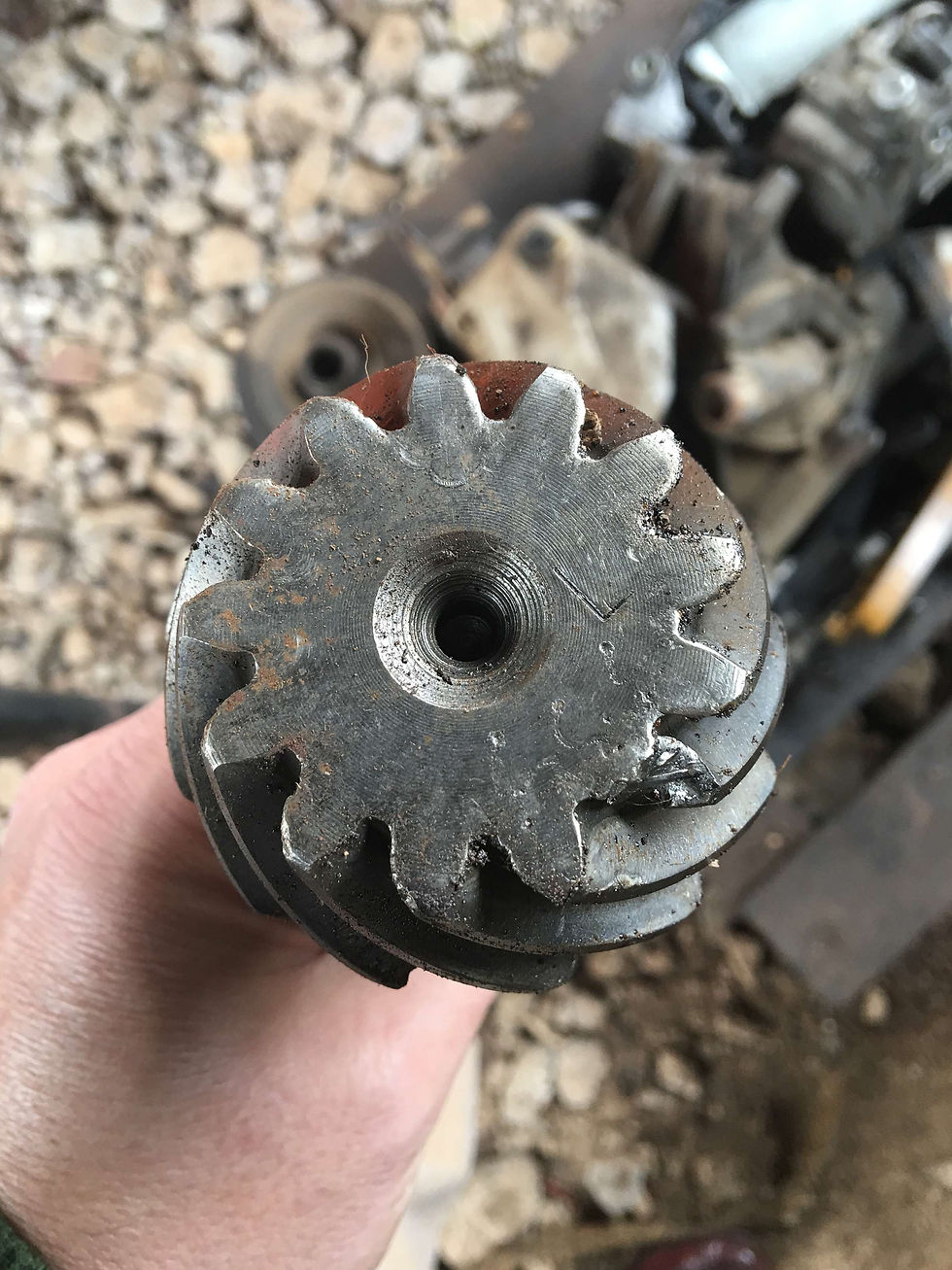
This year we have sent the diffs to the UK, where they have been fitted with new, much stronger pinion and crown wheels and were also professionally set into their cases, including a pegging system that ensure the crown wheel does not flex out of position when under lots of pressure. This is best shown in the following video by Ashcroft
https://www.youtube.com/watch?v=zHi_usC7KGE. This will not be the breaking point in 2018!
Diff Lockers
To understand 4x4 driving, you need to realise that power flows to the least resistance and that you can be stranded with one wheel spinning merrily in sand or the air and the others not moving. To combat this we can lock the prop shafts (front and rear) and the wheels (side to side) together and force power/drive to each wheel independently.
Firstly we have a central locker in the gearbox transmission which we run locked all day, driving front and rear prop shafts. We have had problems in the past with this as it is the original Range Rover air-driven system. We stripped the gearbox and rebuilt it in 2016 and found holes in the pipes. We will relook at this system again this year but any advice on how to secure it better will be appreciated.
For the side to side locking, we have installed a Limited Slip Differential in the front axle. This has a number of small plates inside it which bind together under force and create some locking of the two sides. https://www.youtube.com/watch?v=WeLm7wHvdxQ Whilst this is sufficient for general driving, it is not enough for the really tough stuff.
To get through really loose stuff, climbing out of river beds (see film section of Car 9 climbing the rocks) or steep sandy hills, we have installed locking devices on both front and rear differentials which are operated via electrical switches in the driver’s cab. We have had so many problems with these failing us during the Charge that at times we have considered ripping them out and just throwing them away. However, having replaced the cross-members two years ago, we also found that the oil was not escaping when the lockers were engaged so we then specially lathed a spiral channel in the locking bolt that now allows the oil to drain freely. I am hopeful this is now no longer an issue but we will test the locking mechanism extensively in the weeks to come.
Half Shafts
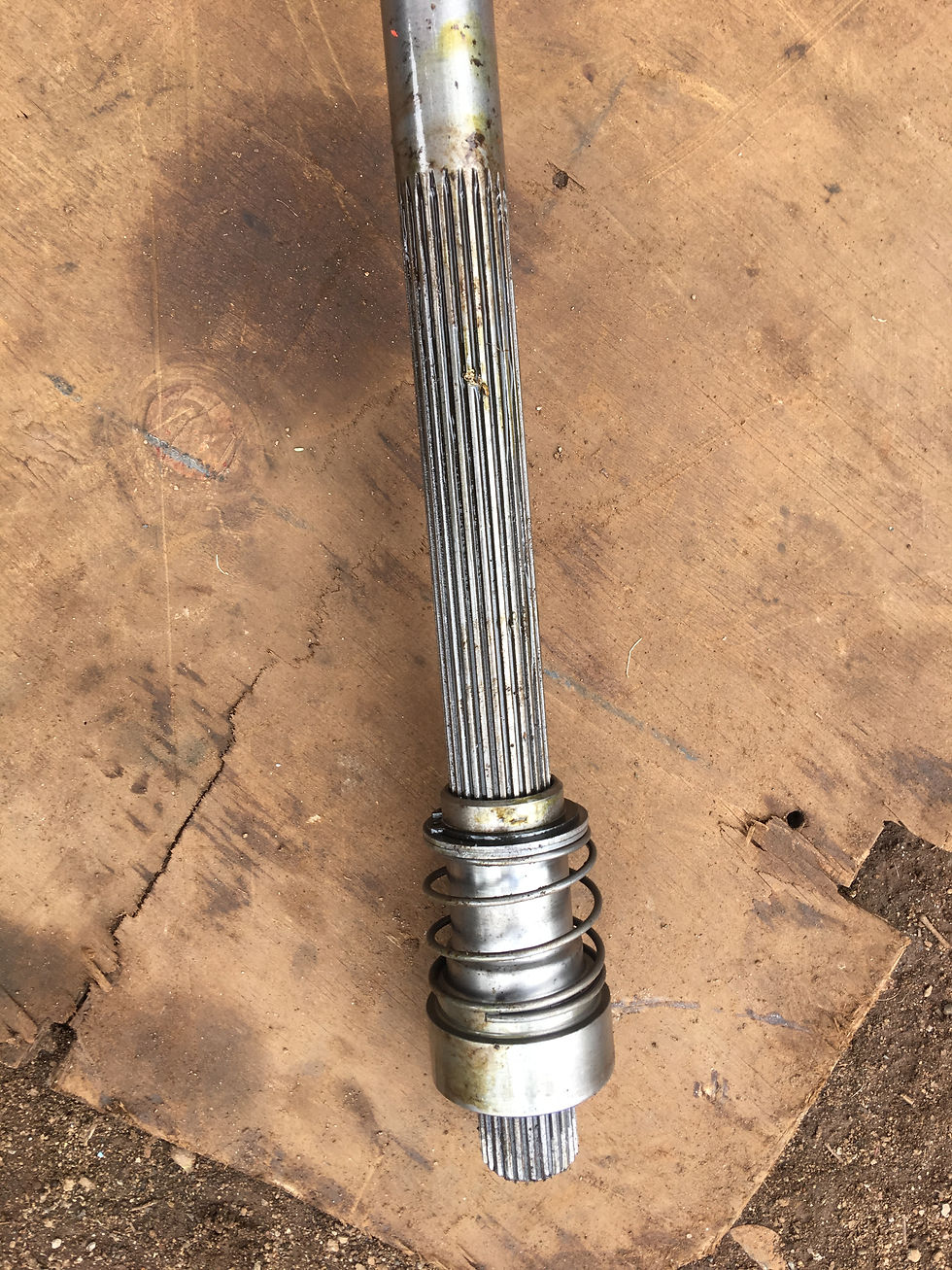
The power is now running horizontally towards the wheels and in standard cars, it is the half shafts that often are the thinnest pieces of metal in the system and under stress they snap. We have therefore upgraded the Falcon's half shafts to competition standard and they are made out of strengthened steel. An extra little trick is that we have employed is to have installed small stub shafts that are purposely weaker than the half shafts. If something needs to break, it can be them and we carry spares to replace them.
We could upgrade the half-shafts to titanium versions if the budget stretches that far.
CV Joints

At the end of front axle, we have CV Joints which swivel as the steering turns. In 2013 we managed to put all the weight on the left front wheel dropping into a small river bed and when power was applied, the left side CV joint shattered. We had only done x3 checkpoints so decided to carry on and do as much a possible by road and achieved 12 checkpoints (finishing in top 20). Our only problem was that the steering couldn’t turn left so whenever we came to a left turn, we had to reverse in right lock and then carry on. As the day wore on and it got worse and worse, we nearly ran off a cliff, thankfully the rear winch cable saved the day. We have since imported strengthened CV joints and fitted them to the car.
Hubs
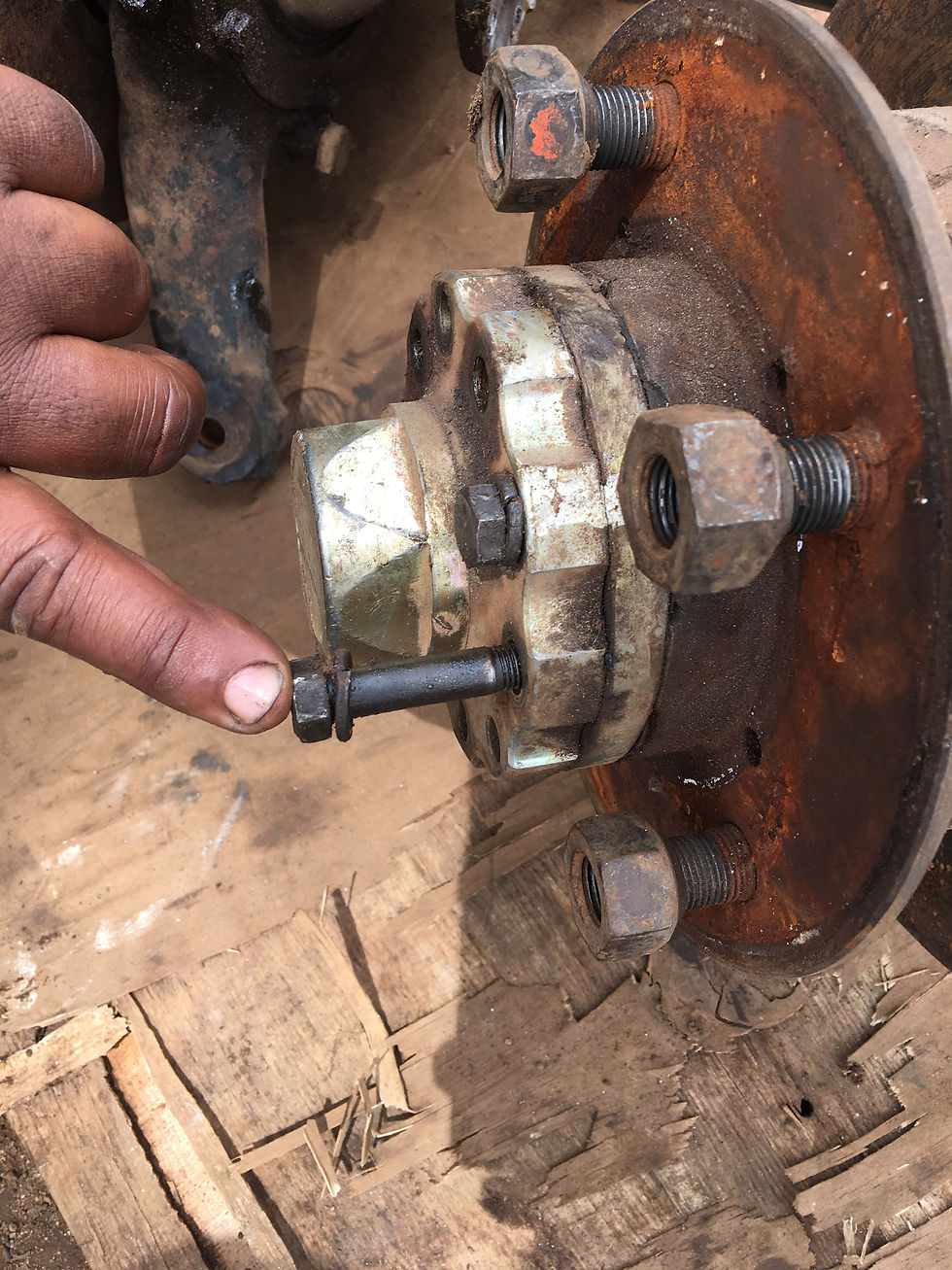
The wheels are attached to the half shafts via hubs. Worried that this was now the weakest point, in 2014 we upgraded the Falcon’s hubs to heavy duty imported versions. They look shiny and gold when clean. When they were fitted, at the last minute, the garage did not tighten the bolts with the proper torque and after 4 checkpoints we heard a nasty ting, ting, ting noise. Stopping to check the problem, we found the rear half shafts, still attached to the hubs, protruding halfway out of the rear axles. Time to head home early again! This year we are going to buy strengthened bolts and ensure they are tightened to the correct torque settings!!
Tyres

2016 saw us invest in bigger 38" tyres to give us more grip and also raise the height of the axles a few inches. The terrain can be sandy and we need more traction which the bigger treads provide. Because we don’t have drop-axles like some of the other cars, we need every inch of lift we can get to climb over the rocks in our path. A lot of time this year has also been spent in increasing the wheel arches as the bigger tyres were in in danger of rubbing against metal work!
So this week we aim to fit the new differentials and get the Falcon out onto the road again. Once she is running and the basics are working, we will bring her back into the shop for tweaks and adjustments before heading out into the bush for some proper testing!
Comments